Workers’ hands are the most commonly injured body part. Whether the hazard comes from rotating machinery, pinches between two materials, heat, chemicals, or electricity, your hands are under constant attack. Without them, every task would be difficult to perform. This article identifies the common hazards and risks to a worker’s hands as well as ways to mitigate injuries and promote safety.
CHEMICALS
Many commonly used chemicals in the workplace can cause chronic illness by way of dermal absorption and may go undetected by the worker. Therefore, direct contact must always be avoided. Some chemicals cause burns on the skin that can be painful and debilitating and may take a long time to heal. Chemical burns and dermal absorption potentially result in serious or even fatal injuries.
Employers and employees must each ensure proper use of gloves specific to the type of chemical being handled. Many materials are used for glove construction; some are better suited than others for resisting breakthrough or permeation.
- Breakthrough time can be determined using an ASTM standardized test for the elapsed time between initial contact of the chemical on one side of the glove material and the analytical detection of the chemical on the other side of the glove material. If there is no breakthrough, the glove is marked ND (none detected). Breakthrough times generally reflect how long a glove can be expected to provide resistance when totally submerged in the chemical.
- Permeability of the material (permeation rate) is how long it takes a chemical to pass through the glove on a molecular level. Glove thickness can affect the permeability of a material. ASTM provides a test, and the glove manufacturer must rate the permeability of the glove on its fact sheet. Always refer to the manufacturer’s fact sheet to determine the correct glove for handling a chemical.
LACERATION/ABRASION/CRUSHING
Cutting a finger while removing insulation, scraping a hand on a sharp panel-door edge, or slamming a finger with a tool can be hard to avoid. Human beings are fallible, but we can minimize the impact of these injuries by using hand personal protective equipment (PPE) such as leather, cotton, or rubberized gloves. In some circumstances, Kevlar or metal gloves may be necessary to provide the highest levels of protection. Leather gloves are the standard protective equipment for all general injuries and are relatively inexpensive.
A good rule of thumb is that gloves will be necessary if a tool is necessary as part of the job. A job hazard analysis, along with good, old-fashioned common sense will help determine the probability of being lacerated or otherwise injured while performing a task. Much like other forms of PPE, gloves must be inspected for damage and wear and replaced as necessary.
Various work methods can go a long way toward reducing preventable hand injuries. For example, instead of using a knife to strip insulation, use a wire stripping tool. Instead of a razor blade or scissors to open letters or boxes, use a safety knife (Figure 1).
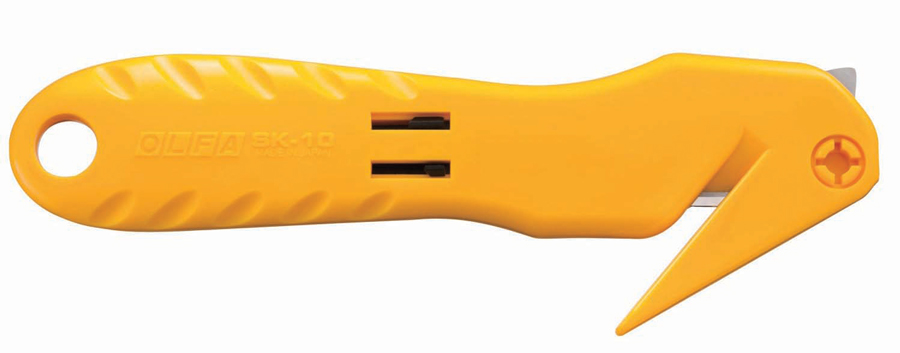
Figure 1: Safety Knife
Maintaining proper guarding on tools such as circular saws or right-angle grinders will reduce the potential for injury. Inspect tools regularly to ensure the guarding has not been removed or compromised. Removing the guard may aid in getting a job done quicker or easier, but it could cost a finger — or worse.
ERGONOMICS AND REPETITIVE MOVEMENT
Carpal tunnel syndrome is one of the most common hand injuries in the United States. It is even harder to prevent when activities outside of the workplace contribute to these injuries. Other common types of repetitive motion injuries include tendonitis and bursitis, which are injuries to tendons and bursae, respectively.
Carpal tunnel syndrome is not an occupational hazard exclusive to those using a computer. In addition to its impact on those who type all day, it is a hazard to anyone who performs repetitive hand motions, mechanical gripping, small-part assembly, or encounters vibration in fields such as mechanics, factory work, or an electrical trade. Education is the best method of prevention for repetitive motion injuries.
To avoid these injuries, perform frequent range-of-motion exercises (Figure 2) to warm up and prevent and alleviate injury.
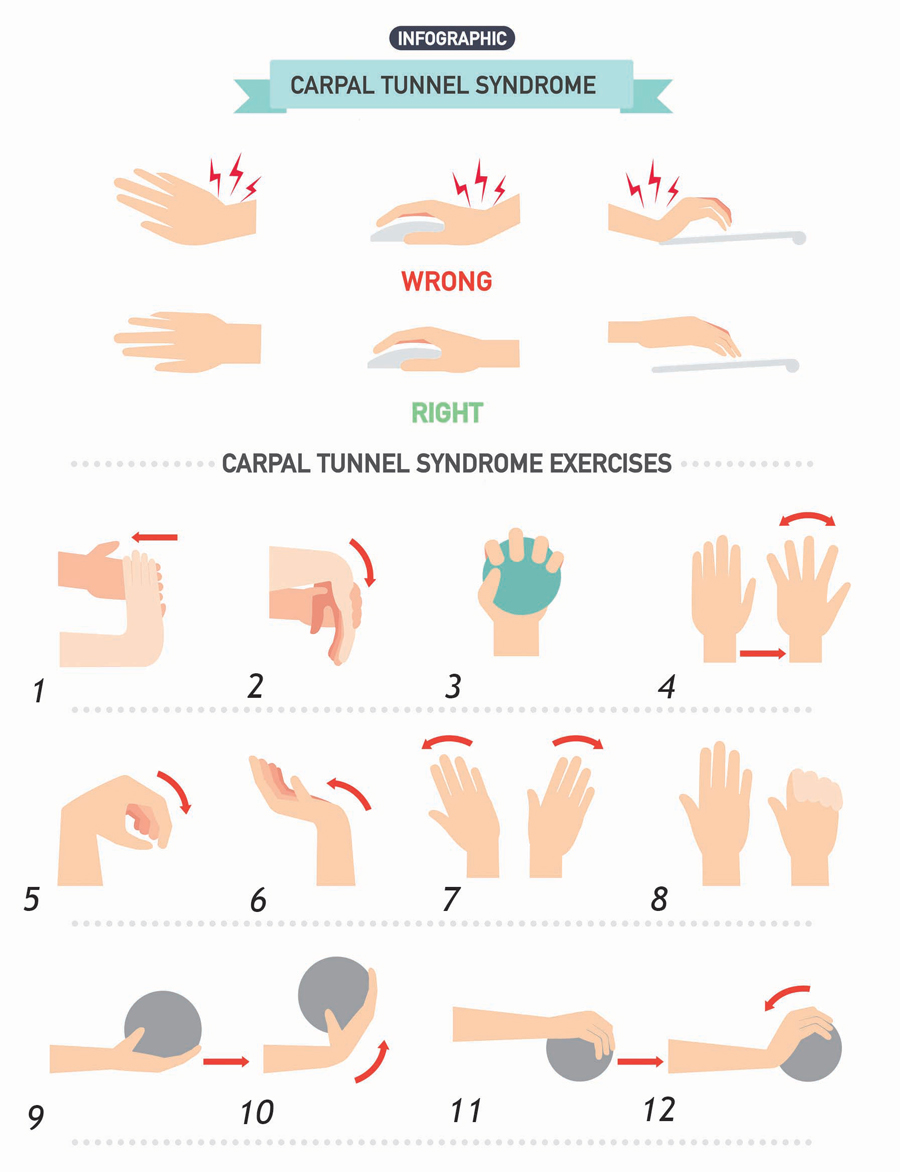
Figure 2: Carpal Tunnel Syndrome Exercises
Many tools are available to promote proper ergonomics and posture, including a wave-style keyboard (Figure 3) or a trackball mouse.
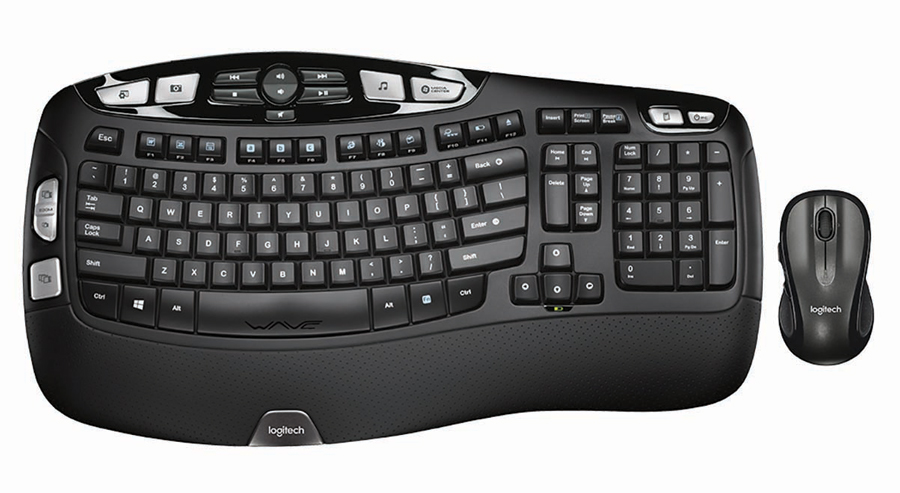
Figure 3: Wave Keyboard
Take a minute or two to get up and move around and stretch for every hour sitting and working on a keyboard. Several manufacturers of ergonomic mice and keyboards have companion software that reminds the worker to stretch and suggests more effective stretching exercises depending on use.
Hand tools such as right-angle power drills and t-handle drivers can provide proper hand positioning, which helps prevent hand and wrist strain. Padded palms and fingers can help prevent repetitive motion injury while using vibrating tools such as a hammer drill or jig saw or while using impact tools such as a hammer.
PROTECTING AGAINST ELECTRICAL SHOCK
Electrical shock injuries to the hands are common in the electrical testing industry. The best prevention for this type of shock is to wear the proper voltage-rated gloves (Figure 4).
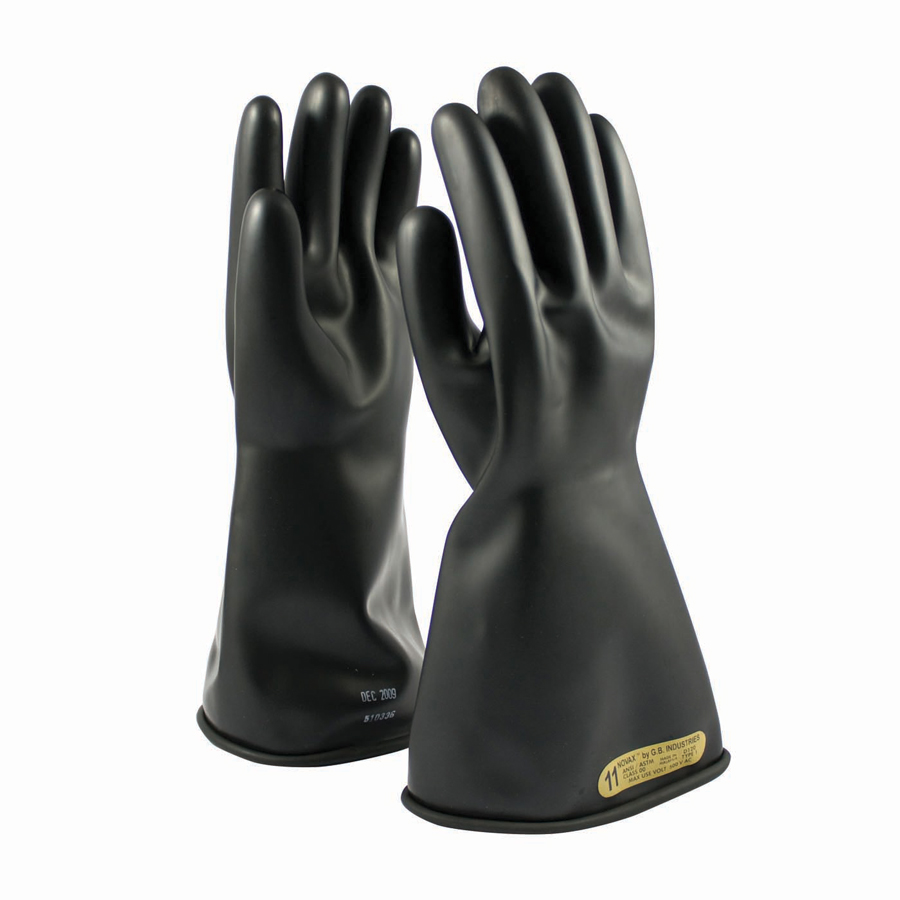
Figure 4: Voltage-Rated Glove
Inspection and Testing
Gloves must be tested using an ASTM standard to ensure they properly protect the worker. The chart from Salisbury (Figure 5) indicates the voltage level where each glove is designed to be used. The cuff length must be adequate to protect the forearm from electric arc.
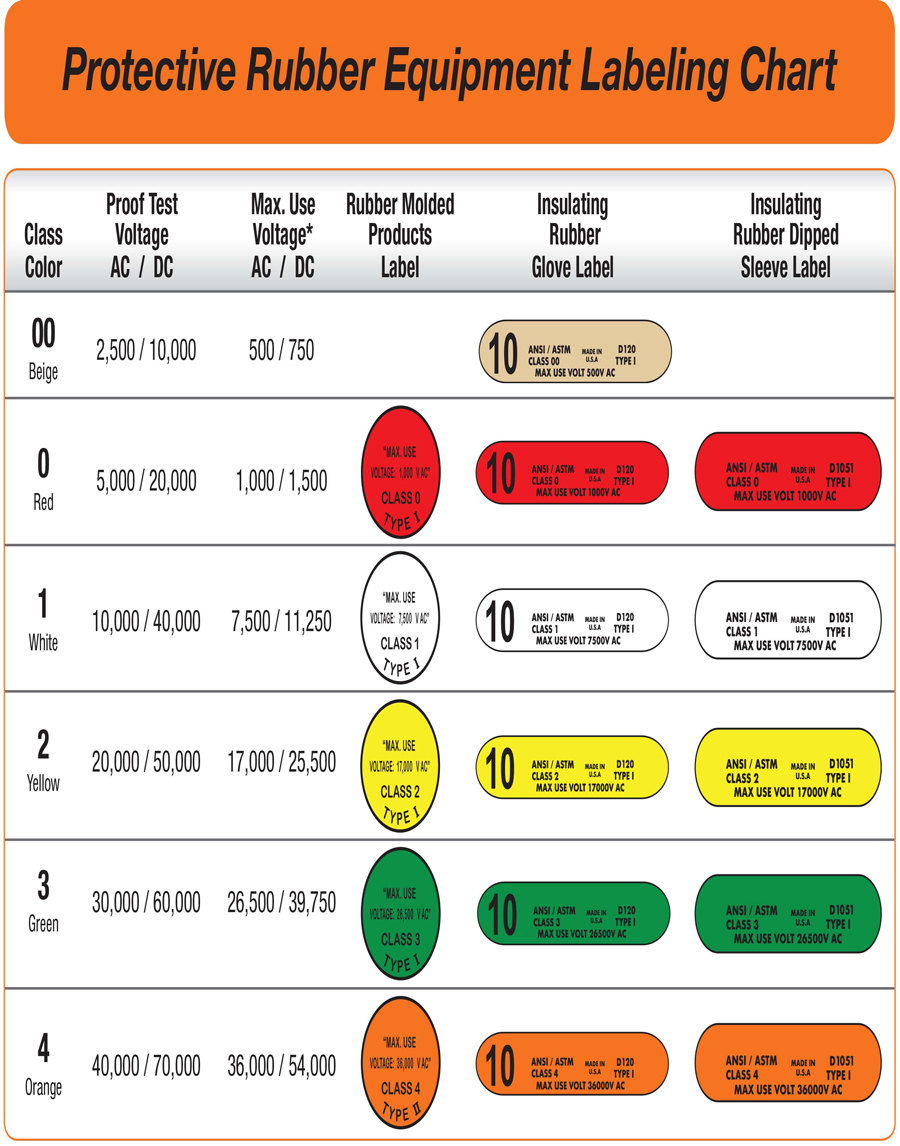
Figure 5: Glove Labeling
Gloves must be regularly re-tested to the ASTM specification. Two OSHA standards indicate the appropriate test intervals:
- OSHA 1910.137, Personal Protective Equipment – Electrical Protective Devices. This regulation states that gloves must be electrically tested before first issue and every 6 months thereafter.
- OSHA 1910.268, Special Industries – Telecommunications. This regulation states that natural rubber insulating gloves must be electrically tested before first issue, 12 months after first issue, and every 9 months thereafter. Any unissued glove that has not been tested within 12 months must be retested before issue to an employee.
The date of last inspection must be marked on the glove or tracked by another means to confirm the expiration date has not been exceeded. OSHA 1910.137(b)(2)(xii) states that the employer shall certify equipment has been tested in accordance with the requirements of paragraphs (b)(2)(viii), (b)(2)(ix), and (b)(2)(xi). The certification must identify equipment that passed the test and the date it was tested. Individual marking of the glove (i.e. equipment identification numbers) and entering the results of the tests and the dates of testing onto a tracking log is an accepted means of meeting this regulatory requirement.
Users must inspect PPE before each use and after any action that may cause damage. This inspection does not need to be tracked, but it does need to be conducted by the user to ensure their safety. The user must visually inspect the gloves for any physical damage such as punctures, cuts, knicks, cracks, scratches, or abrasions. The user must also inspect the glove for any chemical deterioration of the material by looking for swelling, softness, stickiness, or hardening.
Ozone may also cause rapid deterioration of rubber goods. The glove must be inflated to no more than twice its normal size to ensure the rubber stretches, and the glove must be inspected for breaks in the material by listening and looking for a defect. If a portable inflator is not available, the glove can be manually inflated by rolling the cuff towards the fingers and spreading the fingers to look and listen for escaping air from holes.
This procedure should be repeated with the glove turned inside out to ensure a thorough inspection. Additional detailed inspection guidelines and procedures can be found under ASTM F1236, Standard Guide for Visual Inspection of Electrical Protective Rubber Products.
CONCLUSION
With so many bones, ligaments, tendons, and joints keeping hands and wrists working, there is ample opportunity for injury in the workplace and during everyday activities. Proper protection, training, equipment, and techniques go a long way to protecting these important assets.
Paul Chamberlain has been the Safety Manager for American Electrical Testing Company Inc. since 2009. He has been in the safety field since 1998, working for various companies and in various industries. He received a Bachelor of Science from Massachusetts Maritime Academy.