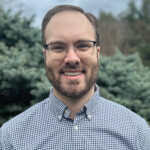
This issue of NETA World’s “Insight and Inspiration” series features Eric Goetz, a Technical Trainer at Qualus Services LLC, a NETA Accredited Company headquartered in Lake Mary, Florida. Eric’s main responsibilities are creating and delivering training classes to Qualus employees and their clients. He also leads the Qualus University (QualU) new-hire bootcamp training program for apparatus testing technicians and assists with relay technician and design engineer new-hire bootcamps.
Eric recently accepted the opportunity to lead the design and build-out of two training labs: an apparatus testing lab in Louisville, Kentucky, and a utility relay lab at headquarters in Lake Mary, Florida. These training facilities will be leveraged for hands-on activities during their training seminars and internal training programs.
Goetz graduated from the University of Louisville with a BS in electrical engineering and an MEng in electrical engineering. He is a licensed Professional Engineer in the state of Kentucky and has achieved NETA Level 4 Certified Senior Technician.
Here, Goetz describes his journey and shares his thoughts for those new to the industry.
NW: How long have you been in the field, and what was your path to your current position?
Goetz: I have been in this field for the past ten years. While in college, I interned in the maintenance department at a local power plant. I started with Qualus as a field engineer right after graduating from college. When I first started, I assisted with all types of electrical testing and maintenance work, but I picked up on relay testing pretty quickly, and that became my main role during outages. Once I got the hang of relay testing, I started getting involved in the protection and controls check-out portion of commissioning projects.
Relay upgrades, switchgear commissioning, and NERC testing became the majority of my work. Once I had a few years of experience as a field engineer, I asked if I could also start doing the design work for the relay upgrade projects we were supporting out of our office. My field experience taught me what worked and what didn’t work when it came to relay upgrades, so the design side came naturally to me.
Several years ago, I began helping our training department, QualU, by instructing during internal training programs and delivering our power systems seminars at client sites. When our training department found out I wanted to transition out of the field, they asked if I would be interested in becoming a technical trainer. I always enjoyed delivering training classes and had a lot of ideas for new training content for our employees, so I immediately jumped on the opportunity to join the QualU team. The training role has been a change of pace compared to the field, and one of my biggest fears was losing my technical edge, but my knowledge of testing and the power industry as a whole has continued to increase as I have helped develop our training programs.
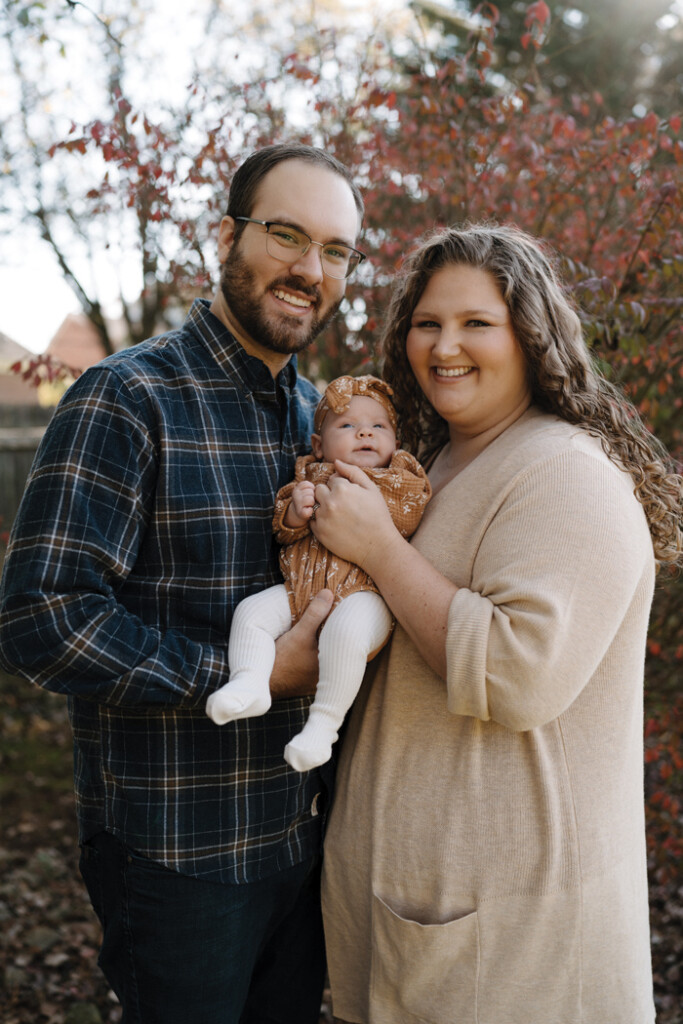
NW: What attracted you to electrical testing?
Goetz: I wasn’t very familiar with the world of electrical testing when I was looking for a job towards the end of college. I had always imagined I would end up working at a power plant since that’s what my grandfather, father, and brother did. I wasn’t having much luck finding a full-time role at the power company I was interning with, but one of my classmates had just been hired by Qualus and told me they were looking for more new graduates. I reached out to a Qualus salesman I had met while interning and talked to him about the company. Most of what he told me about the job went right over my head at the time, but I knew they worked in power plants, so I figured it would be a good way to get experience for one day getting a job at a plant.
Like a lot of people in this industry, I had stumbled into a job in testing. Ten years later, I have no regrets about pursuing this career. I have been fortunate to work for a company that didn’t put me in a box and allowed me to do design jobs and deliver training while I was still a field engineer. I tell people who are interviewing for our new-hire bootcamp programs that this industry is far from overpopulated. As long as you put in the hard work, you can quickly make a name for yourself and move up the ranks.
NW: Who influenced or mentored you along the way?
Goetz: I have been fortunate to have a variety of mentors along the way. Most of my time in the field has been spent alongside technicians. At the power plant, I was placed with the electric shop technicians for my first semester to help them with PMs and outage work. They taught me about the plant systems by actually working on them. They also helped shape my personality and made me less like a stereotypical engineer. You need thick skin and a good sense of humor to work in the field, and they definitely helped me with that.
When I started with Qualus in the Louisville shop, our technicians taught me the ins and outs of equipment testing and maintenance. They taught me how to run the tests, and I would use what I had learned in school to help figure out the “why” behind it all. Technicians are still my go-to resource when I want to know how things are done in the real world versus how they are described in books and manuals.
I have also had some great engineering mentors. Some of them have directly mentored me by making sure I worked alongside them on challenging jobs early in my career. I have also learned a lot from design engineers by testing and commissioning their projects and paying attention to the choices they made. Every job is a learning opportunity if you try to understand the “why” behind a design instead of just going through the motions.
NW: What about this work keeps you committed to the profession?
Goetz: I became an engineer because I like fixing problems. It can be extremely challenging, but also extremely rewarding. In this job, every problem I help fix improves the reliability of our customers’ equipment and the safety of their systems. While some electrical testing tasks can seem mundane compared to others, all of our work revolves around catching and fixing problems with equipment before it blows up and ensuring that the devices responsible for clearing a fault work properly. You can only trust the PPE requirements listed on an arc flash label if the breakers upstream are well-maintained and have the correct settings. If we don’t do a thorough job, those breakers may fail to operate during a fault, and someone could get hurt.
NW: Describe one of your best workdays…what happened?
Goetz: One of my best days started with waking up to a bunch of missed calls from one of our technicians. I called him back, and he told me a local flood pumping station had one of its 4 kV motor buses trip offline and they needed help getting it back online. This station in particular had been upgraded a few years prior and had never really been through a major flood event, so this was the first time it was running close to capacity. I arrived at the site and pulled all of the event files and determined that the trip was caused by an issue with the PT circuits. This made the relay think there was a reverse power event, tripping out the main.
Once that issue was fixed and the plant was online again, we were told that other flood pumping stations were having trouble with some of their motors, and we mobilized to fix those problems. For the rest of the day, I bounced from one flood pumping station to the next, troubleshooting motor problems and getting them back online. It was a hectic day, but it was also very satisfying because not only was I fixing problems, but I was also directly helping the city I lived in. Our customer reached out afterward and said that my efforts had increased their flood pumping capacity by millions of gallons.
NW: Please share the story of a day that didn’t go as planned. How did you respond, and what did you learn?
Goetz: A lot of days out in the field don’t go exactly as planned, but one day in particular sticks out. We were on the second day of a relay upgrade project at a power plant. The first few days of a long project are nerve-racking because they typically set the tone for the rest of the project. I had been put in charge of both the design and the installation, which added another layer of pressure since any problems with the design or execution would point back to me. The first day had been slow-moving, which is normal, but we were beginning to gain some steam on the second day. After lunch, another field engineer, a subcontracted wireman, and I were wiring up some switchgear doors when I heard a hard hat hit the floor. I turned around to see the wireman having a seizure. This was the first time I had ever seen a seizure, so it took me a second to process what was even happening. I remembered from first aid training that the main thing you can do for someone during a seizure is try to make sure they don’t hurt themselves, so I cleared the wireman’s tools out of the way and pulled him away from the switchgear cubicle he was working in.
A contractor from another electrical testing company went to get onsite EMS, and I sent our other engineer out to find the wireman’s co-worker in another area of the plant. Within a few minutes, the plant’s emergency response team was in the room to assess the situation and loaded him onto a stretcher. Thankfully, the wireman didn’t suffer any serious injuries and only needed a couple of days of rest to recover.
I am fortunate in a way since that is the worst medical emergency I’ve had to deal with onsite. One thing that stood out to me was how everyone in the area worked together to help during the emergency. You hear it all the time that we are our brothers’ and sisters’ keepers out there, but you don’t fully understand how important that concept is until something bad happens. Our team, the contractor from the other testing company, and the onsite emergency response team all worked together to help someone during an emergency.
NW: Which energy trend do you think will most affect your work in the future?
Goetz: Data centers and electric vehicle charging are two rapidly growing customer bases that involve unique electrical equipment. There is a need for training that revolves around the electrical testing and maintenance of these systems by NETA technicians as well as the safe operation of these systems by their owners. I look forward to working with the subject matter experts in our company to help develop this training.
NW: If you were talking to a young person interested in becoming an electrical testing technician, how would you describe the job, and what advice would you give them?
Goetz: When I interview candidates for our new-hire training programs, half of the interview is spent trying to explain exactly what we do. I tell them that this job is something new every day. One day, you might be working at a power plant; the next day, you are working at a steel mill. One day you could be working on transformers and the next you are testing breakers. It is going to take you a few years to start seeing the big picture, but once everything clicks, you will be able to pull up to pretty much any industrial site and have a good idea of what kind of electrical equipment is inside based off the products leaving the site and the power lines coming into it.
I can especially relate to people in engineering school who are interviewing for a job in the field because I was in their shoes ten years ago. Something I saw happening throughout engineering school was that a lot of my classmates became disillusioned as they began interning because they saw that many engineering roles are more about project management or designing systems that you would never work on yourself, and less about actually being the one who goes out and fixes stuff. My internships at the power plant had me working alongside maintenance technicians, so I had a decent mix of hands-on and desk work.
The best part of the job was when I was the one who figured out how to fix a problem. Those times made me feel like I was actually contributing and not just watching. When I started as a field engineer for a testing company, it became my job to find problems and fix them, so I had inadvertently stumbled into a career that allowed me to constantly do what I had always imagined engineers did.
NW: Is there a question you wish we had asked?
Goetz: Yes. I would ask how you continue to make sure you are always learning and never becoming stagnant while in the field.
I strongly suggest constantly getting out of your comfort zone and volunteering to help out on projects that involve tasks or equipment that you might not be familiar with. The jobs will be challenging and frustrating at times, but that is a great way to grow and not become pigeonholed into only working on one type of equipment.
I am also a firm believer that the best way to truly learn something is by teaching it to others. Several times when I’ve been training someone new and they ask me why we do something a certain way, I realize that the only reason I do it that way is because that was how I was taught. Once I dig a little deeper into the “why” behind it, I find there might be different and sometimes better ways of doing it.