Prelude and Overview
The electrical power services market should see tremendous growth over the next five years. The legal and regulatory requirements, the need for qualified electrical workers, and the requirement that the workers are properly trained and educated are paramount. When it comes to electrical safe work practices, the use of NFPA 70E as a roadmap to success is critical. To learn more, read on…
Tariffs and trade wars be damned — in the electrical power services industry, you hear it every day: “We don’t have enough people.” “The workload outpaces the workforce.” “We need more qualified people.” It goes on and on….and what does that do to us, as an industry, to make sure we fulfill the production requirements placed upon us to meet the demand?
And how do we get to where we need to go and accomplish our goals without getting our electrical workers seriously injured or killed?
NFPA 70E®, Standard for Electrical Safety in the Workplace®, is more than just a book. Let’s examine the situation, the challenges, and the importance of using NFPA 70E to meet our aspirations of providing an injury-free workplace for all of our people.
Editor’s note: 70E® and Standard for Electrical Safety in the Workplace® are registered trademarks of the National Fire Protection Association, Quincy, MA.
PART 1: THE FUTURE
Electrical Infrastructure: A Partial View and Insight into the Next Five Years
Recently, we met with our local investor-owned utility, Oncor Electric, to discuss a 112-year-old entity called the Dallas Electric Club (DEC). The DEC is a nonprofit organization established as a networking group to foster peer-to-peer collaboration in the electrical power and energy industries. (Shameless plug: Check them out at www.dallaselectricclub.org.)
The scope of Oncor/DEC meeting was to increase involvement with regional players in the utility services industry, as we recognize that we all need to band together to handle the upcoming electrical power needs of our customers and end users. It was from that meeting that an interesting discussion item came up: Earlier in 2024, Oncor announced a five-year CapEx budget of approximately $24B.
Twenty-four billion (with a B) dollars — now that’s a ton of electrical infrastructure and services that must be engineered, procured, installed, commissioned, and maintained, and all with high expectations of performance and execution from a first-class investor-owned utility serving a large portion of the State of Texas.
But that wasn’t the highlight of the discussion. It was what Oncor had recently announced as a change to their 2025 CapEx plans: a 150% overall increase to their budget, which is now $36.1B (again, with a B!). The change was driven by many factors, including artificial intelligence, data center buildout, large commercial and industrial load growth, system resiliency, and other factors…along with the fact that Texas is a great place to move your business. (Another shameless plug!)
It was from that discussion that another thought emerged: If Oncor has a $36.1B CapEx budget, what about other electric utilities across North America — or is it just a Texas thing?
So, by doing a little research, the following additional five-year anticipated CapEx trends were discovered. As a word of caution: This is not a deep dive into perfectly validated data. Rather, it is quick research to see whether other utilities were anticipating the same trends. Please understand the basis of the information and data. For a CapEx summary, see Table 1.
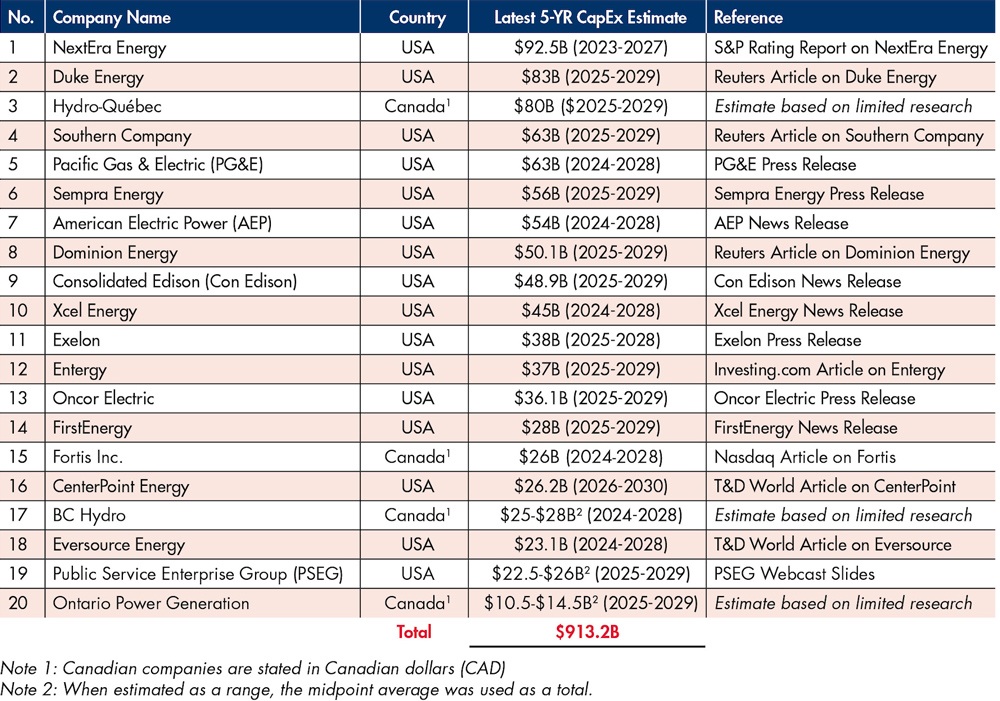
The table is a look at the five-year CapEx budgets for 20 of (arguably) the more prominent utilities in North America, most of which are in the United States, with a few in Canada, understanding the following clarifications and data limitations:
Data Limitations: Comprehensive five-year CapEx budgets (e.g., 2024–2028 or 2025–2029) for all utilities are not always publicly disclosed in full detail. We used the most recent multi-year plans that were available, typically sourced from company reports, regulatory filings, or industry analyses like those from the Edison Electric Institute (EEI), S&P Global, Deloitte, or the U.S. Energy Information Administration (EIA).
Currency: U.S. utilities are in USD; Canadian utilities in CAD, unless converted for consistency.
As you can see, the estimated investment over the next five years for just these 20 utilities, taking into account the differences in U.S. and Canadian currencies, is approximately USD 900 billion.
Imagine what the full number looks like when you throw in every utility, every project, every state and province. It’s massive. It’s exciting. But it also raises a red flag, and it’s worth repeating the opening statements:
“We don’t have enough people.”
“The workload outpaces the workforce.”
“We need more qualified people.”
And it’s not just a hiring problem, it’s a training and safety problem. Electric utilities, data centers, semiconductor fabs, refineries, automotive plants, steel and paper mills, along with just about any heavy commercial or industrial load, all have one common goal and message for the providers of services: Do it with a high expectation of performance and do it error- and injury-free.
Because here’s the truth: If we rush to meet demand without properly preparing our people, we’re going to pay the price in injuries, delays, and even lives.
PART 2: THE REGULATORY SIDE
OSHA and Enforcement of Laws
I mentioned this at PowerTest25 in Orlando, and repeated it several times during the conference:
“If one mistake could cost you your life — or
take you away from your family forever —
what would you do differently today to
stay safe?”
That one hits hard. Because in this line of work, the danger is real. One shortcut. One oversight. One wrong assumption…and it can all go sideways in a heartbeat.
After an incident occurs, it’s often like the old Southwest Airlines ad: “Wanna get away?” You probably knew better. You probably had training on the equipment or systems that led to the incident. But. You. Just. Didn’t. Do. It. So we have a challenge for you and all those around you: Do the right thing, each and every time. Change the paradigm, move the cheese, do whatever you have to do, just do it.
It’s the reason why you MUST employ an electrical worker who is:
- Willing to work
- Trainable
- Able to work and train without impairment from drugs or alcohol
Having a workforce that is the most qualified, the safest, and has an eye for attention to detail is a sure-fire formula for success. But it doesn’t come without challenges. I’ve been in the field services arena within the electrical testing and maintenance services business for over 40 years, and I’ve made my share of mistakes. Most of them were not super-impactful, but a few of them were.
And what does this have to do with NFPA70E? Hold on to your shorts (pun intended), we’ll get to it. Let me share two stories — one light, one heavy — but both with lessons.
The “Oops” Moment
In my early days, I was doing a thermographic survey at a plant. I opened the door to a Westinghouse DB-25 breaker with a cell door trip interlock. Boom! The breaker tripped. We closed it back in right away. No harm, no foul, and I moved on. (As a side note, the cell door trip interlock is one of the dumbest accessories Westinghouse ever offered on their low-voltage switchgear lineups.)
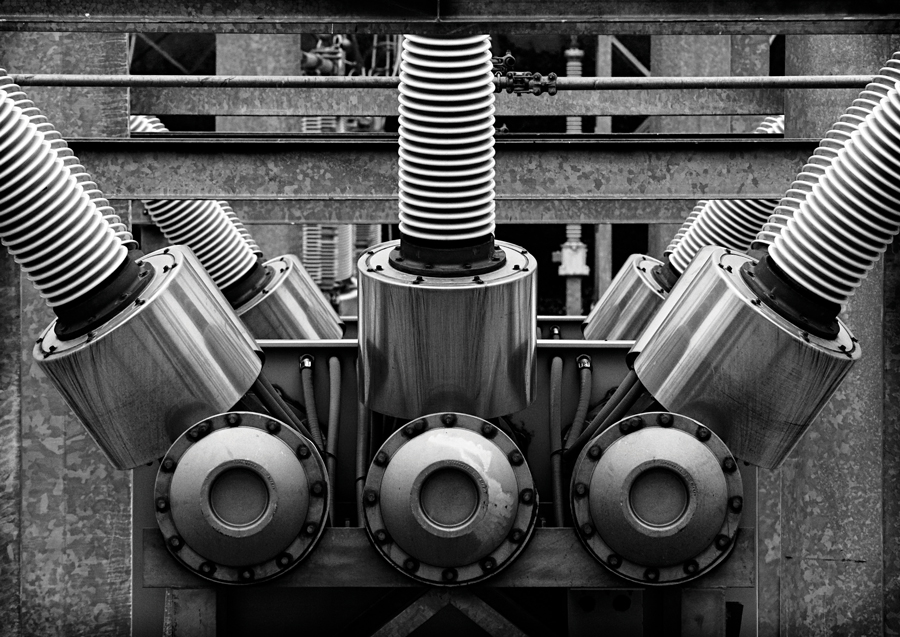
Lesson? The equipment worked as designed, but I didn’t fully respect the system. That’s not a habit to keep.
The Close Call
At a hospital, I stood next to a technician bypassing a 480-volt, 2000-amp transfer switch. A metal rod broke and fell across the bus. Boom! 480-volts arced, metal vaporized, and the room filled with smoke.
But here’s the kicker: We were prepared.
We were suited up with the right PPE. We turned away at the moment of the arc. Nobody got hurt.
That’s not luck — that’s training. That’s NFPA 70E in action.
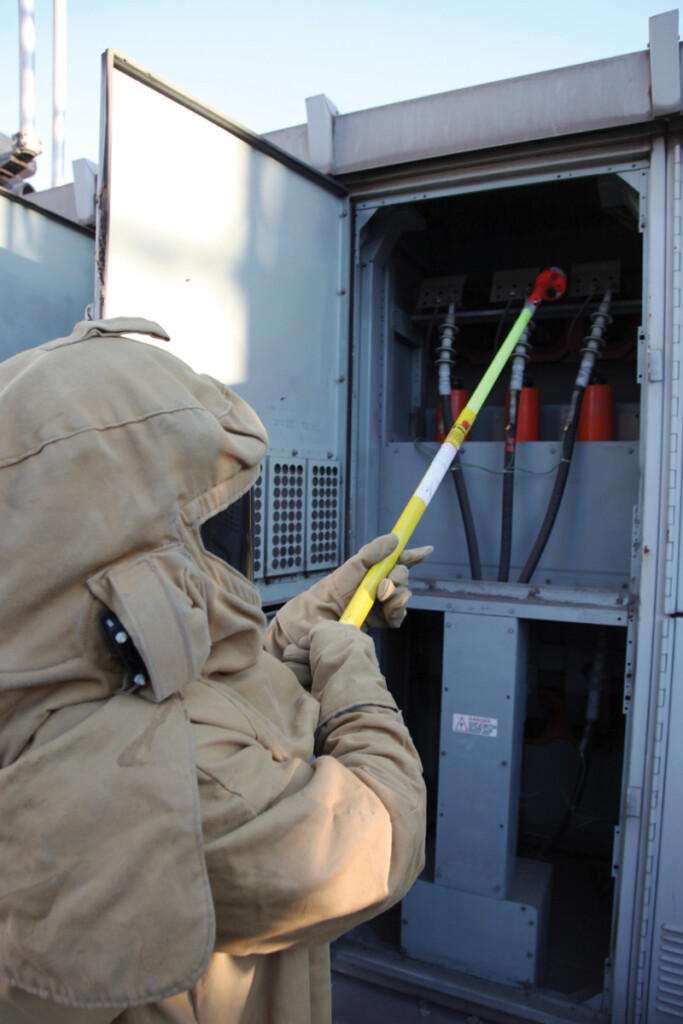
NFPA 70E Impact
What’s the point of these two stories? It’s to illustrate a point. If we, the electrical workers in the field, understand and follow NFPA 70E’s work practices and guidance, we will not only minimize the effects and outcomes of electrical safety incidents, but I would argue we have a good chance to eliminate them altogether.
Sure, electrical equipment is magic, and sometimes the magic smoke gets let out unexpectedly, but even in those scenarios, if you follow the processes and procedures in 70E, the overall impact will be (or should be) minimal.
Now, going back to the beginning and looking to the five-year horizon…why does NFPA 70E matter in all of this?
Quite simply: Qualifications.
“We don’t have enough people.”
“The workload outpaces the workforce.”
“We need more qualified people.”
As employers, we have a responsibility to only allow qualified workers to perform electrical work. Not only is it a moral responsibility, which should be enough, but OSHA requires it as well. And even if you can’t exactly correlate the reasons to a specific OSHA regulation or section, such as 29 CFR 1910, all of it is covered under one simple and prominent section: OSHA’s General Duty Clause, found in Section 5(a)(1) of the OSH Act.
The general duty clause requires employers to provide a workplace free from recognized hazards that are causing or likely to cause death or serious physical harm to employees. Section 5 specifically states:
SEC. 5. Duties
(a) Each employer
- shall furnish to each of his employees employment and a place of employment which are free from recognized hazards that are causing or are likely to cause death or serious physical harm to his employees;
- shall comply with occupational safety and health standards promulgated under this Act.
(b) Each employee shall comply with occupational safety and health standards and all rules, regulations, and orders issued pursuant to this Act which are applicable to his own actions and conduct.
Key points of Section 5 of the OSH Act include:
- Purpose:
The General Duty Clause ensures basic workplace safety when no specific OSHA standard applies to a particular hazard. - Employer Responsibility:
Employers must ensure their workplaces are free from recognized hazards, meaning hazards that the employer or industry knows about or should have known about. - OSHA’s Role:
OSHA can cite employers for violating the General Duty Clause if a recognized hazard exists, the employer fails to take reasonable steps to eliminate or reduce it, and the hazard is causing or likely to cause death or serious harm. - Recognized Hazards:
A hazard is considered recognized if it is of common knowledge or general recognition within the industry, or if the employer knew or should have known of its existence. - Feasible Abatement:
To establish a violation, OSHA must also identify a feasible and practical method to correct the hazard. - Enforcement:
OSHA can cite employers for violating the General Duty Clause if they fail to take reasonable steps to eliminate or reduce recognized hazards that are causing or likely to cause death or serious physical harm.
What does all of this mean? One important aspect is that a qualified electrical worker, who has been properly trained and can demonstrate the requisite skill, is key to complying with OSHA requirements. Now, bring on NFPA 70E.
PART 3: WHY NFPA 70E MATTERS
Use it as a Roadmap to Train Your Employees
Corey Hannahs, Senior Electrical Content Specialist for NFPA, often speaks of the Electrical Cycle of Safety (ECoS) (Figure 1) and the relationship between three important industry standards:
- Electrical installations governed by NFPA 70
- Electrical maintenance governed by NFPA 70B
- Protection of electrical workers governed by NFPA 70E
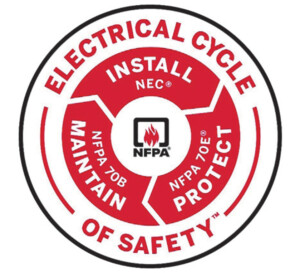
SOURCE: NFPA – REPRINTED WITH PERMISSION
The concept is quite simple, actually. Each component addresses a different requirement for overall safety of electrical power systems: the design and install, the required maintenance, and protecting the workers in and around it all. It stands to reason, “If even one piece is missing, it could result in preventable accidents that put people, property, and critical processes at risk.”
To access NFPA’s fact sheet on ECoS, go to www.nfpa.org/electricalcycleofsafety.
Earlier I told you to hold on to your shorts, and here’s why: With the inevitable upcoming Boom! in the electrical power services industry, the requirements to provide a safe and error-free workplace and qualified employee base, you must have the right people, and you have to train them on the essential requirements of their job.
In this article, we won’t address the day-to-day production aspects of an electrical worker’s job, which is different for each person. But we can address the ability for someone to safely perform work on or around energized electrical conductors or circuit parts. How so? Follow the requirements and train your employees on NFPA 70E.
Here’s just one example of what you can do for some of the more basic electrical tasks.
Task: Testing for the Presence of Voltage on an Energized Panel
Why this matters: Testing for voltage is a super-common task, but also one of the most dangerous moments if done wrong. Let’s say you are approaching a 2,000-amp, 480-volt switchboard, and you need to test for the presence of voltage. Here’s some suggested guidance on what to do (courtesy of NFPA 70E):
Perform a risk assessment:
- Can this be done de-energized (except when testing for voltage)?
- What are your arc flash and shock boundaries?
Follow these sections:
- 110.6 Test Equipment
- 130.4 Shock Risk Assessment
- 130.5 Arc Flash Risk Assessment
- Annex I Job Briefing Checklist
Use the right tools:
- Rated meters, insulated tools
- Test-before-touch approach
Wear the proper PPE (Assuming Cat 2 Exposure):
- Arc-rated clothing, hard hat, safety glasses, hearing protection, rubber insulating gloves with protectors, leather footwear
Bottom line: Routine doesn’t mean risk-free. Training and repetition save lives.
This example is just one way to use NFPA 70E in your electrical safety training activities. Because the standard is a work practices document that is revised every three years through the ANSI consensus standards-making process, you can be assured it is topical, relevant, and the most informative out there. The new editions immediately supersede the previous ones, and you aren’t grandfathered into a previous version. Stay on top of it, build a library of tasks and procedures for your employees, share them and use them often, and you will see continuous improvement in the safety-related aspects of your business.
FINAL THOUGHTS
We’re heading into a five-year surge like this industry hasn’t seen in decades. The work is coming. The money’s flowing. The pressure is mounting.
The question is: Will your workforce be ready?
Because when it comes down to it, having the right people doing the right thing safely is your biggest competitive advantage.
So start now. Train your teams. Build your playbook. Make NFPA 70E the heartbeat of your safety culture, because it really matters.
And remember this simple truth:
- Before you work on it, turn it off.
- Test before touch.
- And above all — respect the hazard.
- You’ll be glad you did.
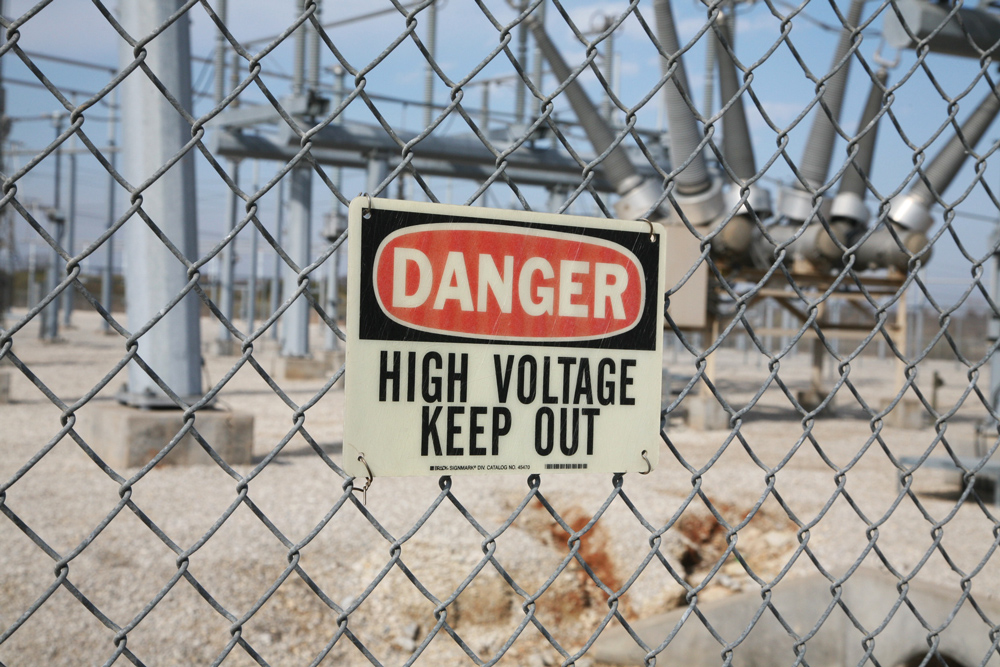
REFERENCES
- National Fire Protection Association (NFPA). NFPA 70E–2024®, Standard for Electrical Safety in the Workplace®. Quincy, MA. https://www.nfpa.org/codes-and-standards/nfpa-70e-standard-development/70e.
- Occupational Safety and Health Administration (OSHA), 29 CFR 1910.269, Electric Power Generation, Transmission, and Distribution Standard. Available athttps://www.osha.gov/laws-regs/oshact/Section5-duties.
- National Fire Protection Association (NFPA). NFPA Electrical Cycle of Safety. Available at https://www.nfpa.org/education-and-research/electrical/nfpa-electrical-cycle-of-safety.
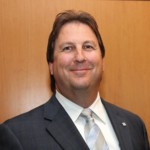
Ron Widup is the Vice Chairman, Board of Directors, and Senior Advisor, Technical Services for Shermco Industries and has been with Shermco since 1983. He is a member of the NETA Board of Directors and Standards Review Council; a Principal member of the Technical Committee on Standard for Electrical Safety in the Workplace (NFPA 70E); Principal member of the National Electrical Code (NFPA 70) Code Panel 11; Principal member and Chairman of the Technical Committee on Standard for Competency of Third-Party Evaluation Bodies (NFPA 790); Principal member and Chairman of the Technical Committee on Recommended Practice and Procedures for Unlabeled Electrical Equipment Evaluation (NFPA 791); a Principal member of the Technical Committee Standard for Electrical Equipment Maintenance (NFPA 70B); and Chair of IEEE Std. P902 (Yellow Book) Recommended Practice for Maintenance and Operational Safety of Electrical Power Distribution Systems in Industrial and Commercial Facilities.He is Chairman of the Texas State Technical College System (TSTC) Board of Regents, a NETA Certified Level 4 Senior Test Technician, State of Texas Journeyman Electrician, a Senior Member of the IEEE Standards Association, and an NFPA Certified Electrical Safety Compliance Professional (CESCP).