As humans, many people feel they are invincible — until they aren’t. The electrical industry is filled with individuals with tremendous ability to do their jobs. Whether you are an engineer designing an electrical system, an electrical contractor managing the installation, an electrician installing the electrical system, or a manager overseeing workplace electrical safety for an employer, you play a significant role in your safety and that of others.
Confidence in your ability is a good thing unless it grows into an arrogant bravado that leads you to complacency. Getting the job done should never be done at the risk of rolling the dice on your personal safety. Being versed in the safe work practices found in NFPA 70E®, Standard for Electrical Safety in the Workplace®, can assist those in the electrical industry in building a conscientious confidence to perform their jobs safely and return home each night.
While others can have some level of impact on jobsite electrical safety, the focus here is on the roles of the employer and the employee. These two roles are responsible to ensure that employees go home safely each night based on the direct decisions they make. You could even say they have a specific duty to one another to help ensure jobsite safety.
Employers and employees must have awareness and knowledge of NFPA 70E safe work practices in order to make impactful decisions in maintaining electrical safety while work is being performed on the jobsite. Through that, conscientious confidence can be built, allowing employers and employees to be secure that the decisions they make are the right ones and are aligned with keeping people safe when working around electrical hazards on the jobsite.
THE EMPLOYER ROLE
Without question, an employer has a legal and moral obligation to keep their employees safe on the job. When considering how citations, litigation, hospital bills, and increased insurance premiums can all follow impactful electrical incidents, having a financial responsibility to the company might even be added to the employer obligation list.
From a legal standpoint, businesses that operate within the United States of America are subject to meeting the regulations of the Occupational Safety and Health Act of 1970 (OSH Act) as administered by the Occupational Safety and Health Administration (OSHA). Not doing so is likely to result in costly penalties. The General Duty Clause found in Section 5 of the OSH Act requires that each employer:
- shall furnish to each of his employees employment and a place of employment which are free from recognized hazards that are causing or are likely to cause death or serious physical harm to his employees[1]
- shall comply with occupational safety and health standards promulgated under this Act [1]
While these are legal obligations established for the employer to meet, it should also be noted that a portion of the General Duty Clause also puts the onus on the employee. Part (b) of the General Duty Clause requires:
…each employee shall comply with occupational safety and health standards and all rules, regulations, and orders issued pursuant to this Act which are applicable to his own actions and conduct[1].
So there is truly a legal obligation for the employer as well as the employee to comply with OSHA regulations.
There is also a direct tie between OSHA and NFPA 70E that dates back to the original development of the standard. OSHA regulations tell an employer what is expected of them in keeping their employees safe, but they do not necessarily provide information on how to accomplish doing so. This apparent gap was recognized by the National Fire Protection Association® (NFPA®), and in May 1975, an offer of assistance to develop a new standard tailored to help fulfill OSHA’s responsibilities and also align with the National Electrical Code® (NEC®) was sent to John Stender, the Assistant Secretary of Labor for OSHA at the time. He responded as follows:
“The concept, procedures, and scope of the effort discussed with my staff for preparing the subject standard appear to have great merit, and an apparent need exists for this proposed consensus document which OSHA could consider for promulgation under the provisions of Section 6(b) of the Act. OSHA does have an interest in this effort and believes the proposed standard would serve a useful purpose.”
The foundation was therein laid for the original development of the NFPA 70E that is used today.
Employer Duties
Having a firm understanding of the tie between OSHA regulations and how NFPA 70E can help employers meet those requirements is a good transition into looking at some of the specific duties for employers based on NFPA 70E. An employer needs a firm grasp of what NFPA 70E requires of them because they are the driving force behind establishing electrical safety in the workplace. They set the policies and procedures that must be followed by the employees and are the ones who must hold them accountable when they aren’t. Building a solid culture from the top of what the expectations are, what support will be provided to employees, and what level of tolerance there will be for unsafe work practices will resonate throughout the entire company.
As an employer, several key requirements within NFPA 70E must be met and prioritized.
Electrical Safety Program
Initially, an employer is required to establish, document, and implement the safety-related work practices and procedures required by NFPA 70E. This is done by developing an electrical safety program (ESP). An ESP must meet the requirements of NFPA 70E but also should address the unique electrical hazards that employees can face on a particular jobsite or by performing a specific task. It is important to understand that an ESP isn’t necessarily a one-size-fits-all approach. While Company A has one facility where employees are exposed to certain electrical hazards based on the specific processes or equipment on site, another facility may have similar but other additional potential hazards because of the specific processes or equipment at that particular site. While developing the ESP, each particular jobsite should be evaluated on a case-by-case basis according to the known hazards. Building an ESP should also be a collaborative effort between those who will help manage the process and those who will perform the hands-on work, using outside experts as necessary to close any gaps.
Training
Once the safety-related work practices and procedures are established and documented within the ESP, it is the employer’s responsibility to ensure that employees are fully trained to identify and mitigate risk while performing any tasks where electrical hazards are present. Not only is training critical for the employee but they must also be able to demonstrate to the employer that they have the skills and knowledge needed to perform the specific tasks. Understanding the training the employee has received and the skill set they demonstrate will help the employer determine whether or not an employee can be considered qualified for a specific task. Remember that each task will require evaluation of who is qualified to perform it, as there is no broad-brush stroke to say that an employee is qualified for every task. Logging which employees are qualified for specific electrical-related tasks in the ESP may prove to be beneficial.
Electrically Safe Work Condition
NFPA 70E also requires that employers establish an electrically safe work condition (ESWC) policy that requires hazard elimination to be the top priority when implementing safety-related work practices. NFPA 70E requires the ESWC to be established when the voltage present is 50 volts or greater and the employee is within the limited approach boundary or interacting with the equipment where there is exposure to an arc flash hazard.
An ESWC is defined by NFPA 70E as a state in which an electrical conductor or circuit part has been disconnected from energized parts, locked/tagged out in accordance with established standards, tested for the absence of voltage, and temporarily grounded for personnel protection if necessary. While lockout/tagout (LOTO), which most workers are familiar with, is part of establishing an ESWC, testing for the absence of voltage is also a crucial step that is likely to expose employees to electrical hazards while doing so. Even though hazard elimination is the priority, employees must understand how to establish an ESWC and manage their risk by testing for the absence of voltage before elimination can be verified and achieved.
Establishing an ESP and including an ESWC policy are two key elements of what NFPA 70E expects from employers. Doing so will also help employers meet a portion of the General Duty Clause from the OSH Act by providing a place of employment that alleviates electrical hazards that could cause death or serious physical harm to employees. Yet, the employer’s confidence in implementing these NFPA 70E safe work practices is only part of the equation; it also takes employees doing their part around electrical safety to solve the problem.
THE EMPLOYEE ROLE
A safe place of employment that is free from negatively impactful electrical incidents cannot be achieved unless employees grow their awareness of NFPA 70E safe work practices and implement that knowledge every day on the job. Doing so will keep the employee safe and will also help mitigate risk for their coworkers.
Employers and employees must both do their part to achieve a high level of electrical safety in the workplace. While the employer is responsible for establishing safe work practices and documenting them within the ESP, NFPA 70E requires employees to comply with those requirements. Ultimately, the employee must be accountable for their personal safety and know their own limitations. That means understanding whether or not they are qualified for the task they are being asked to perform.
Qualified Person
NFPA 70E defines a qualified person as one who has demonstrated skills and knowledge related to the construction and operation of electrical equipment and installations and has received safety training to identify the hazards and reduce the associated risks. Keep in mind that being qualified is on a task-by-task basis and has nothing to do with how many years you have had on the job or the licenses you hold. Based on the specific task being evaluated, a qualified person must be familiar with the equipment being worked on and its operation. They must also have received safety training specific to that equipment so that they can identify any hazards to their well-being and know how to reduce their risk.
As an example, if an employee has been qualified to work within a 120/208-volt branch-circuit panelboard by their employer, that does not make them qualified to work on 480-volt switchgear. Switchgear includes varied hazards, such as fully exposed busbars, that are not present within panelboards. The employer must be the one who determines whether or not an employee is qualified for the task at hand based on the skill they have demonstrated and the training they have received. However, that does not alleviate an employee from speaking up when they feel they are not qualified to perform the assigned task or are not in the right state of mind to do so.
Human Element
The human element of electrical safety must also be factored into safe electrical work practices. It may not be advisable for even a qualified employee to perform a task when other factors may increase their level of risk. Alertness is key to being able to perform work safely and cannot be overlooked or dismissed. Work performed by an employee at the end of a long shift should be held over and performed at the beginning of the next day’s shift or — if that is not possible — completed by another qualified person at the beginning of the next shift.
Pre-planning tasks and shutdowns can help avoid putting employees in a predicament where work must be done when their alertness level is low, sacrificing safety in the process. Illness or other factors, such as being under the influence of legal or illegal drugs or alcohol, also can impact an employee’s ability to perform their work safely. Employers have a responsibility to be aware of their employees’ physical and mental condition, but even then, it may be hard for them to notice some scenarios. Employees must maintain a sense of self and be able to let their employer know if they are not physically or mentally able to perform a task without any potential retribution from their employer.
Informative Annex Q within NFPA 70E addresses human performance as it relates to workplace electrical safety. Although not an enforceable part of NFPA 70E, Informative Annex Q provides great detail on human performance considerations and suggests some ways in which an ESP might be formulated to assist in offsetting these potential negative consequences. Even the most qualified, well-intentioned employee is fallible and can make mistakes, so anticipating and addressing these ahead of time is a good approach to take in keeping the workplace safer.
Attaining Conscientious Confidence
There is a clear difference between attempting a task based upon false bravado and having conscientious confidence to perform the task at hand properly, using the training you have received and the knowledge you have gained to help maintain safety in the workplace. This article builds on some of the key requirements within NFPA 70E for employers and employees, but it does not constitute all that is necessary to fully comprehend and utilize the standard.
Building true conscientious confidence in using NFPA 70E to improve workplace electrical safety requires the appropriate level of training to implement the standard effectively at your company from the standpoint of the employer as well as the employee.
CONCLUSION
When considering all the factors that impact electrical safety — employers, employees, the ESP, the ESWC policy, training, etc. — electrical safety can be viewed as a business system. NFPA has highlighted how holistic electrical safety can be achieved by using NFPA 70E, combined with NFPA 70®, National Electrical Code® (NEC®), and NFPA 70B, Standard for Electrical Safety in the Workplace, by implementing the Electrical Cycle of Safety™ (ECoS™).
In his bestselling book, The 7 Habits of Highly Effective People, author Stephen Covey stated, “If you put good people in bad systems, you get bad results. You have to water the flowers you want to grow.” What do you think, is it time to water the flowers?
REFERENCES
- Occupational Safety and Health Administration (OSHA). OSH Act of 1970. General Duty Clause, Sec. 5. Duties. Available at: https://www.osha.gov/laws-regs/oshact/section5-duties.
- NFPA. The Electrical Cycle of Safety™. Available at https://www.nfpa.org/ECoS.
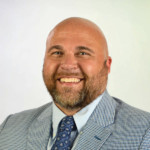
Corey Hannahs is a Senior Electrical Content Specialist at the National Fire Protection Association (NFPA). In his current role, he serves as an electrical subject matter expert in the development of products and services that support NFPA documents and stakeholders. Corey is a third-generation electrician, holding licenses as a master electrician, contractor, inspector, and plan reviewer in the state of Michigan. Having previously held roles as an installer, owner, and executive, he has also provided electrical apprenticeship instruction for over 15 years. He serves on the technical committees for UL 2272, Electrical Systems for Personal E-Mobility Devices, and UL 2849, Electrical Systems for Ebikes. Corey was twice appointed to the State of Michigan’s Electrical Administrative Board by former Governor Rick Snyder and received United States Special Congressional Recognition for founding the B.O.P. Building Opportunities for People (B.O.P.) Program, which teaches construction skills to homeless and underprivileged individuals.